Grasping Welding WPS Specifications: Ideal Practices and Techniques for Top Quality Welds
In the world of welding, grasping Welding Treatment Spec (WPS) requirements is an essential component that straight affects the high quality and stability of welds. Complying with these requirements ensures uniformity and integrity in welding end results. Nonetheless, achieving quality in welds exceeds merely understanding the requirements; it entails applying ideal practices and methods that elevate the craft to a level of precision and skill that distinguishes the standard from the phenomenal. As we navigate with the intricacies of welding WPS criteria, revealing key understandings and methods for accomplishing top-tier welds will be paramount for welders looking for to master their craft and produce welds that stand the test of time.
Recognizing Welding WPS Criteria
Understanding WPS requirements is important for welders, designers, and examiners involved in welding operations. By adhering to WPS guidelines, welders can create welds that fulfill the required mechanical homes and structural integrity. Assessors depend on WPS documents to verify that welding treatments are being followed appropriately and that the resulting welds are of excellent quality. Designers utilize WPS requirements to design welding treatments that make certain the toughness and dependability of bonded frameworks.

Important Devices for Quality Welds
Grasping welding WPS criteria is vital for welders to efficiently use the crucial tools needed for creating quality welds. The type of welding machine needed depends on the welding procedure being used, such as MIG, TIG, or stick welding. Cord brushes and damaging hammers are important for cleansing the weld joint before and after welding to remove any contaminations that might impact the top quality of the weld.
Secret Techniques for Welding Success
To accomplish welding success, one have to understand the vital methods vital for producing top notch welds. Maintaining a stable welding and a stable hand placement throughout the process is crucial to attaining precision and uniformity in the Clicking Here welds. By understanding these crucial strategies, welders can elevate the top quality of their job and accomplish welding success.
Ensuring Conformity With WPS Requirements
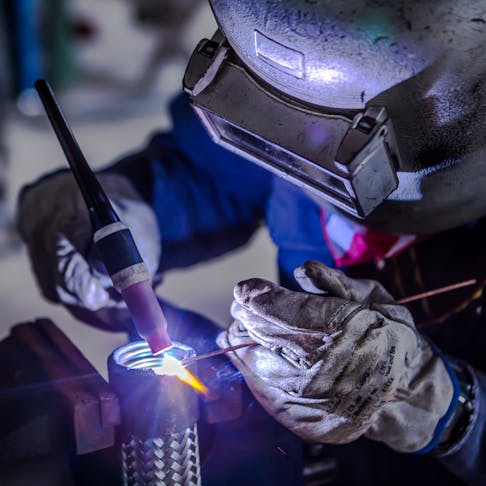
In addition, keeping thorough documents of welding specifications, tools calibration, and assessment results is vital for demonstrating conformity with WPS criteria. By diligently adhering to WPS requirements, welders can ensure that their job fulfills the required top quality levels and contributes to the total success of the welding job.
Troubleshooting Common Welding Issues
When encountered with typical welding issues, determining the source is crucial for effective troubleshooting. One widespread issue is the visibility of porosity in welds, frequently triggered by pollutants such as dampness, oil, or rust. To address this, making sure proper cleansing of the base metal prior to welding and using the right protecting gas can substantially lower porosity. Another concern often encountered is absence of fusion, where the weld fails to correctly bond with the base material. This can stem from inadequate heat input or incorrect welding technique. Adjusting specifications such as voltage, cord feed speed, or take a trip speed can help improve fusion. Additionally, distortion, splitting, and spatter are usual welding challenges that can be mitigated through appropriate joint preparation, regular warm control, and choosing the proper welding consumables. By completely understanding these common welding concerns and their source, welders can efficiently repair issues and attain high-quality welds.
Final Thought
Finally, grasping welding WPS requirements requires an extensive understanding of the guidelines, utilizing necessary tools, and implementing crucial techniques for effective welds. Guaranteeing compliance with WPS standards is crucial for creating quality welds and avoiding common welding issues. By adhering to finest practices and methods, welders can accomplish reliable and constant lead to their welding projects.
In the realm of welding, mastering Welding Procedure Specification (WPS) requirements is an important part that straight affects the quality and integrity of welds.When delving right into the realm of welding methods, a additional info critical aspect to comprehend is the value and intricacies of Welding Treatment Requirements (WPS) requirements. WPS criteria give a thorough guideline for welding procedures, guaranteeing uniformity, high quality, and safety and security in the welding process. The type of welding device required depends on the welding process being utilized, such as MIG, TIG, or stick welding.Achieving welding success with the proficiency of essential strategies requires an extensive understanding and adherence to Welding Procedure Specification (WPS) criteria.
Comments on “Welding WPS Explained: Secret Parts and Perks for Your Welding Processes”